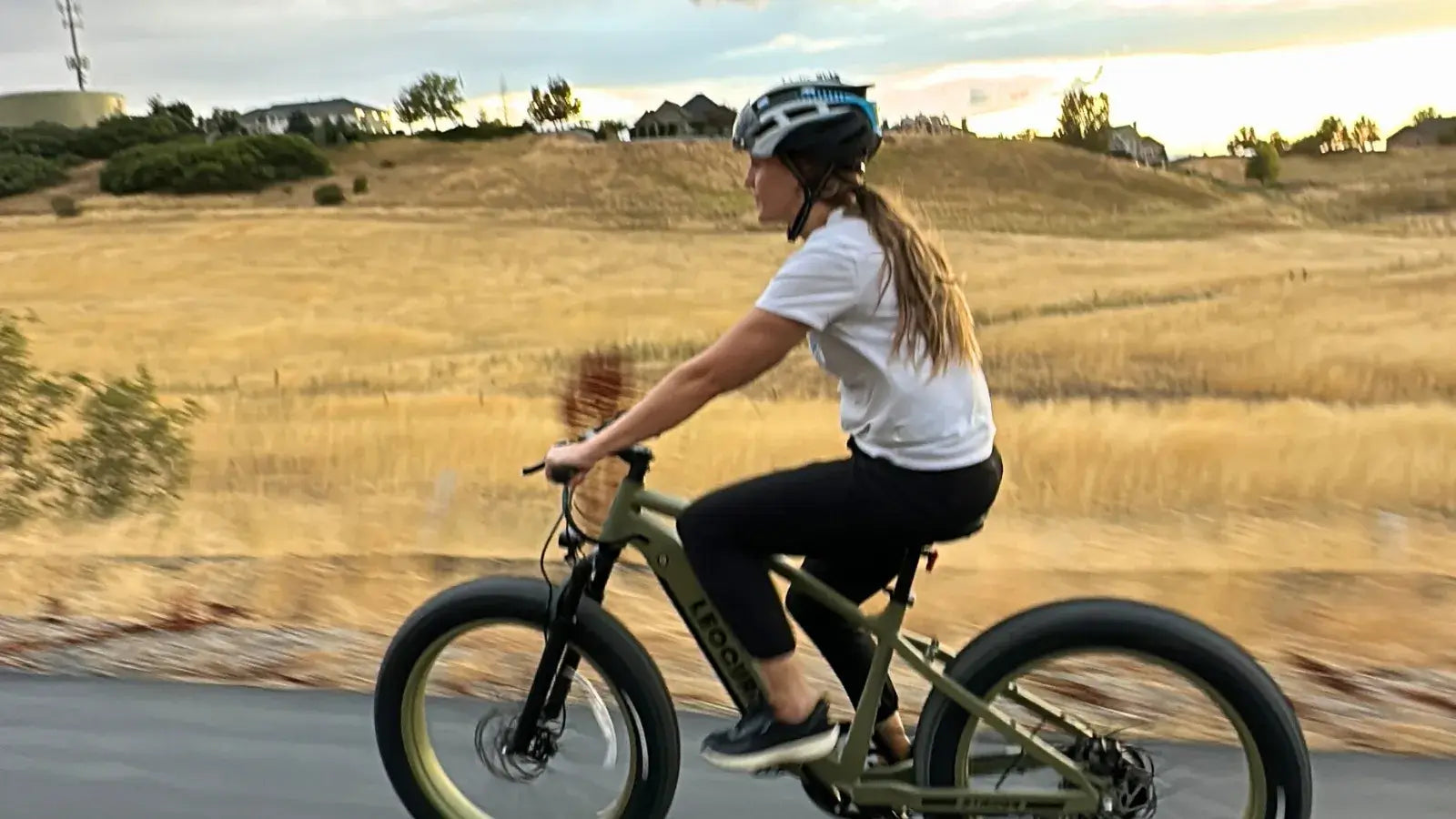
Permanent Magnets in Electric Bike Motors: The Key to High Performance?
The motor is the heart of every electric bike, but what's powering that motor's performance? Inside each electric bike motor, there's a crucial component called a permanent magnet. Although it might seem small and simple, this magnet has a big impact on the motor’s efficiency, performance, and cost.
In this article, we'll cover the common types of permanent magnets used in electric bike motors, explain clearly how engineers select magnet specifications, and discuss future trends shaping magnet technology in the electric bike industry.
Types of Permanent Magnets in Electric Bike Motors
1. Neodymium (NdFeB) Magnets
Neodymium magnets, also known as NdFeB magnets, are currently the most popular choice for electric bike motors. These magnets are made from a powerful combination of rare-earth metals—neodymium (Nd), iron (Fe), and boron (B)—giving them remarkable magnetic properties.
-
High Magnetic Strength: Their maximum energy product ((BH)max) reaches between 35 and 52 MGOe (Mega Gauss Oersted), making them the strongest commercially available permanent magnets.
-
Excellent Resistance to Demagnetization: NdFeB magnets have high coercivity, which means they maintain their magnetic strength even under tough operating conditions.
-
Stable Performance at High Temperatures: By adding elements like dysprosium (Dy) or terbium (Tb), these magnets can handle higher temperatures without losing efficiency.
Practical Advantages for Electric Bikes
Thanks to their strong magnetic properties, NdFeB magnets help electric bike motors become smaller and lighter while still maintaining high efficiency. For example, using NdFeB magnets in a typical 500W hub motor can reduce its weight by around 20%-30% compared to traditional magnets. At the same time, motor efficiency improves by approximately 3%-5%, making rides smoother and extending battery life.
Current Market Overview
In electric bike motors, the most commonly used magnet grades range from N38 to N45, providing a good balance between performance, cost, and reliability.
2. Ferrite Permanent Magnets
Ferrite permanent magnets are ceramic magnets made from compounds of iron oxide and either strontium or barium, and they do not contain any rare-earth elements.
-
Lower Magnetic Strength: Ferrite magnets have a magnetic energy product of 3-5 MGOe, which is around 1/10th the strength of neodymium magnets.
-
Good Demagnetization Resistance: These magnets have solid resistance to losing their magnetism under different conditions.
-
Excellent Corrosion Resistance: Ferrite magnets don’t need any special surface treatment to stay durable and effective.
-
Affordable Price: These magnets are much cheaper, costing only about 1/5th to 1/10th of the price of neodymium magnets.
Applications
Ferrite magnets are commonly used in budget-friendly electric bike motors. Since their magnetic power is lower, motors with ferrite magnets tend to be 30%-50% larger to produce the same power as those with neodymium magnets. However, with recent improvements in motor design, some newer ferrite motors are reaching performance levels close to older neodymium motors.
Market Insights
Around 60% of low-cost electric bikes feature ferrite motors, especially in developing markets. In recent years, the performance of ferrite motors has been significantly improved through better motor designs, such as adding more poles and optimizing the magnetic circuit.
3. SmCo Magnets
Samarium cobalt (SmCo) magnets are another type of rare-earth permanent magnet, made from a mix of samarium (Sm) and cobalt (Co). They come in two main types: SmCo₅ and Sm₂Co₁₇.
-
Strong Magnetic Performance: SmCo magnets offer a magnetic energy product of 15–32 MGOe, lower than neodymium but still very strong.
-
Excellent Temperature Stability: These magnets can operate in extreme heat, withstanding temperatures of 250–350°C, far beyond what neodymium can handle.
-
High Corrosion Resistance: SmCo magnets naturally resist corrosion and usually don’t require any surface coating.
-
High Cost: They are more expensive than neodymium magnets, which limits their use in cost-sensitive applications.
Where They’re Used
SmCo magnets are rarely used in regular electric bikes due to their high cost. Instead, they’re found in specialized applications that demand extreme reliability or high heat resistance—like military-use or industrial electric bikes operating in harsh environments. For everyday riders, these magnets are usually overkill.
4. AlNiCo Magnets
AlNiCo magnets, made from aluminum (Al), nickel (Ni), and cobalt (Co), are among the earliest developed permanent magnets. They still occasionally appear in vintage or retro-style electric bikes.
-
Moderate Magnetic Strength: Their magnetic energy product is around 5–10 MGOe, offering medium strength.
-
Low Resistance to Demagnetization: AlNiCo magnets easily lose magnetism compared to modern magnets, making them less reliable.
-
Stable at Higher Temperatures: They maintain their magnetic performance well under heat.
-
Easy to Shape and Machine: AlNiCo magnets are easy to process into different shapes.
Current Market Status
Because of their lower performance and tendency to lose magnetism, AlNiCo magnets have been largely phased out from modern electric bike motors. Today, they're found only in specialized applications or bikes designed intentionally with a vintage or nostalgic feel.
How Magnet Grade and Specs Are Chosen for Electric Bike Motors
1. Choosing the Right Magnetic Energy Product ((BH)max)
The magnetic energy product, often written as (BH)max, is one of the key specs for permanent magnets. It tells us how much magnetic energy the magnet can store—and it directly affects the power density of the electric bike motor.
What to Consider:
-
High-Power Electric Bikes (500W and above): These motors usually require higher-grade neodymium magnets, such as N40 to N45, to deliver the necessary performance in a compact size.
-
Low to Mid-Power Electric Bikes (250W–350W): For smaller motors, N35 to N40 magnets are typically enough to meet the power needs.
-
Ferrite Motors: Since ferrite magnets have a lower energy product, the motor design has to increase the magnet size to compensate and achieve the same power output.
Finding the Right Balance
While a higher (BH)max allows for a smaller, more compact motor, it also comes with higher costs and can sometimes reduce the magnet’s resistance to demagnetization. That’s why there’s usually a “sweet spot” in motor design.
For most electric bike motors, magnets in the 38–42 MGOe range offer a good balance between performance, size, cost, and durability.
2. Coercivity (Hc): Preventing Demagnetization
Coercivity measures how well a magnet resists losing its magnetic strength (demagnetization). It’s especially important in electric bike motors because these motors often face tough operating conditions like high temperatures or heavy loads.
-
Operating Temperature: For neodymium magnets, coercivity drops by roughly 0.5%–1% for every 1°C increase in temperature.
-
Armature Reaction: High currents create reverse magnetic fields, potentially causing permanent demagnetization.
-
Dynamic Demagnetization: Rapidly changing magnetic fields at high motor speeds can also reduce magnet performance.
Design Recommendations
Magnets should have high enough coercivity to withstand demagnetization caused by armature reactions under the highest expected operating temperature. For electric bike motors using neodymium magnets, intrinsic coercivity (Hcj) should generally be at least 15 kOe. In hotter operating conditions—like brushless motors that can reach 100–120°C internally—an even higher coercivity rating (≥20 kOe) is recommended.
3. Remanence (Br): Maximizing Torque Output
Remanence measures the magnet's residual magnetism and directly affects the strength of the magnetic field in the motor’s air gap, thus impacting torque output.
-
Higher Remanence: Magnets with higher remanence can deliver stronger torque, but designers must balance this carefully with coercivity.
-
Optimized Magnetic Circuit: Better magnet circuit designs can help fully leverage the magnet’s remanence.
-
Typical Range: For electric bike motors, neodymium magnets commonly have remanence values of 1.2–1.4 T.
Real-World Application
High-performance electric bike motors often use "high-Br" neodymium magnets (e.g., Br > 1.35 T) combined with longer axial magnet lengths. This design approach achieves higher torque without increasing the motor's external size, providing riders with powerful performance while keeping the motor compact.
4. Temperature Stability: Keeping Electric Bike Magnets Reliable
Magnets in electric bike motors are sensitive to temperature changes, which significantly impacts reliability, especially when riding in different climates.
-
Neodymium (NdFeB) Magnets:Remanence (Br) drops about 0.12% per °C.Coercivity (Hcj) drops about 0.6% per °C.
-
Ferrite Magnets: Generally have better temperature stability compared to neodymium magnets.
Solutions
- Use Magnets with Better Stability: Select neodymium magnets improved with additives like dysprosium (Dy) or terbium (Tb) for reduced temperature sensitivity.
- Design Safety Margins: Build in temperature compensation margins during motor design.
- Real-Time Temperature Management: Integrate temperature sensors and control systems to adjust motor operation dynamically, ensuring consistent performance.
5. Corrosion Resistance: Protecting Magnets from Harsh Conditions
Electric bike motors operate in challenging environments, often facing moisture, rain, and salt spray, making corrosion resistance crucial.
-
Neodymium Magnets: Usually require protective coatings such as nickel, zinc, or epoxy resin to prevent corrosion.
-
Ferrite Magnets: Naturally resistant to corrosion without additional coatings.
-
Coating Selection: Choose coatings based on cost-effectiveness and environmental conditions.
Industry Standards
Typically, magnets should withstand at least a 96-hour neutral salt spray test. Premium electric bike motors often aim for over 200 hours of corrosion resistance.
6. Mechanical Strength: Ensuring Durability Under Stress
Permanent magnets experience various mechanical stresses during both assembly and regular use in electric bike motors.
-
Bending Strength: Neodymium magnets typically have around 250 MPa but are relatively brittle.
-
Hardness: Ferrite magnets are harder but even more brittle than neodymium magnets.
-
Thermal Expansion Compatibility: Matching the magnet’s thermal expansion characteristics with other motor materials helps prevent mechanical issues.
Design Recommendations
Use mounting methods that avoid stress concentrations.
Precisely calculate the interference fit during magnet installation to prevent cracking or damage under mechanical stress.
Balancing Cost and Performance in Electric Bike Magnets
1. Material Costs: What You Pay for Different Magnets
When choosing magnets for electric bike motors, understanding the cost differences is crucial:
- Neodymium (NdFeB) Magnets: Prices fluctuate significantly due to rare-earth market changes, typically around $50–100 per kg.
- Ferrite Magnets: Prices are stable and low, around $5–10 per kg, making them ideal for budget-friendly bikes.
- Samarium Cobalt (SmCo) Magnets: Expensive, typically costing $100–200 per kg, suitable only for specialized, high-reliability applications.
2. Evaluating Overall Costs: More Than Just Material Price
The cost-effectiveness of magnet choice goes beyond just material price:
- Compact Design Benefits: Higher-performance magnets (like neodymium) can reduce motor size, saving money on other components and materials.
- System-Level Savings: Using higher-priced magnets might lower total system costs by simplifying designs or reducing maintenance.
- Lifecycle Costs: Consider the lifespan, reliability, and maintenance expenses of magnets when calculating long-term costs.
3. Smart Strategies for Optimizing Cost and Performance
To get the best balance between performance and cost, engineers often use these strategies:
- Segmented Power Levels: Choosing magnet types based on power ratings, such as ferrite for lower-powered electric bikes and neodymium for high-performance models.
- Hybrid Magnetic Circuit Designs: Using high-quality magnets only in key motor areas, while employing lower-cost magnets elsewhere to balance performance and expense.
- Recycling and Material Substitution: Researching ways to recycle magnets or substitute with more affordable materials to further reduce overall costs.
What’s Next for Electric Bike Magnet Technology?
1. Magnets with Less Rare-Earth Metals
Manufacturers are finding new ways to build powerful magnets without relying on expensive rare-earth elements by:
-
Using new production methods to reduce rare-earth use.
-
Creating strong magnets that don't need heavy rare-earth materials.
-
Optimizing the magnet’s structure for better performance.
2. Discovering New Magnet Types
Scientists are looking at fresh options for magnets, such as:
-
Iron-Nitride (FeN) magnets (strong and rare-earth free)
-
Nano-composite magnets (tiny particles combined for higher strength)
-
Exchange-coupled magnets (mixing materials for better performance)
3. Designing Magnets and Motors Together
Companies now design magnets and motors as one combined system by:
-
Using computer modeling to build better motors.
-
Simulating real-world conditions to improve performance.
-
Creating digital versions ("digital twins") to test designs virtually.
4. Environmentally Friendly Magnets
Sustainability is becoming a priority with efforts to:
-
Improve recycling methods for magnets.
-
Design magnets that can be easily removed and reused.
-
Use manufacturing methods that produce less pollution and carbon emissions.
Summary
Choosing magnets for electric bike motors is all about balance—finding the sweet spot between power, cost, and durability. As technology keeps improving and environmental concerns grow, the future points to magnets that use fewer rare-earth materials, deliver better performance, and are kinder to the planet.
Leave a comment