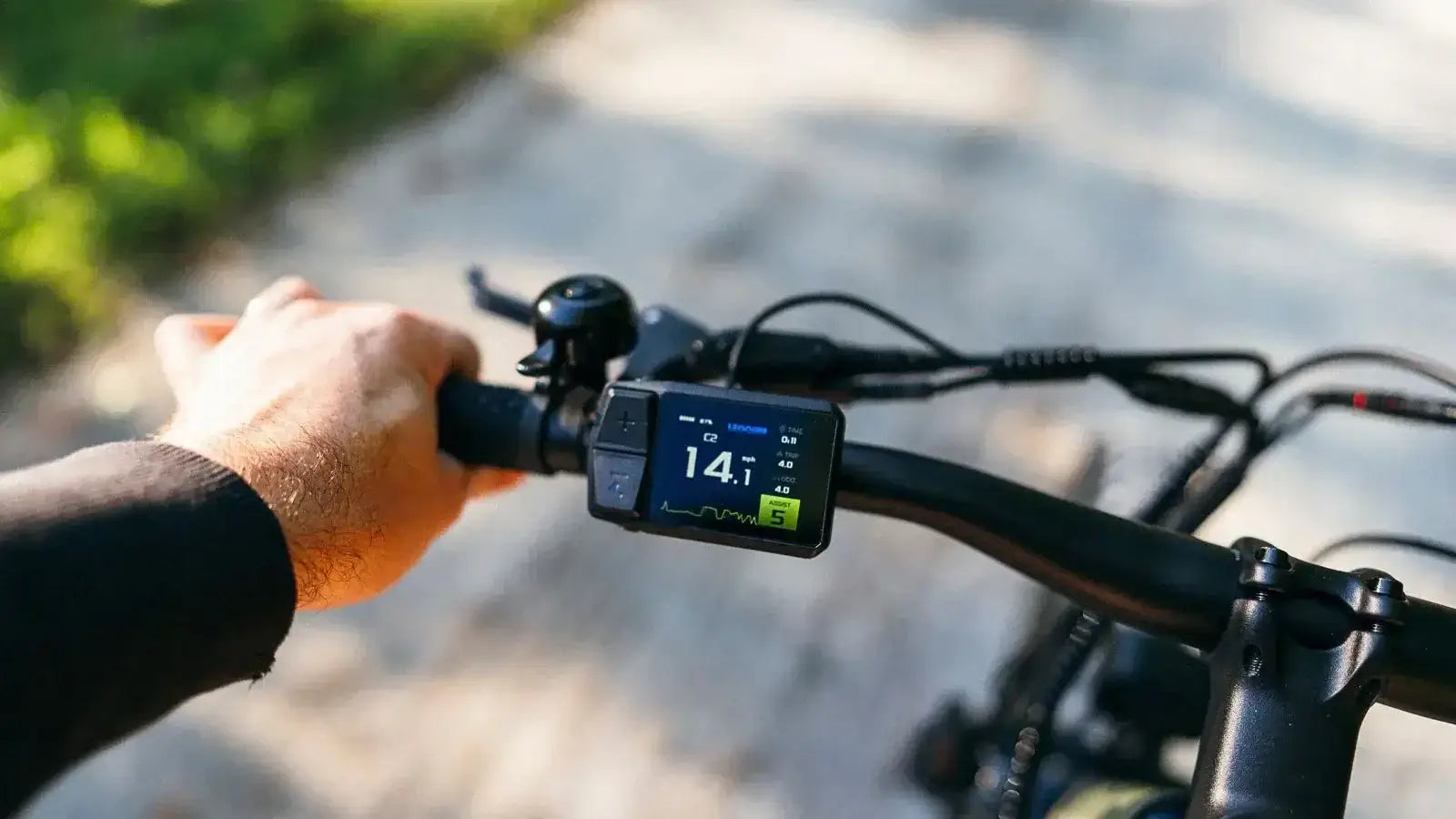
Understanding Ultrasonic Welding in Electric Bike Displays: A Simple Guide
When it comes to electric bike manufacturing, the display panel plays a key role in how users interact with their bike. The quality of its assembly directly impacts the bike’s reliability and user experience. Traditional methods like mechanical fastening and glue are being replaced by the more advanced ultrasonic welding technology.
In this article, we’ll take a closer look at ultrasonic welding in electric bike displays, explaining how it works, its benefits, and how it's being used in the industry.
What is Ultrasonic Welding?
Ultrasonic welding is a process that uses high-frequency vibrations (usually between 15kHz and 70kHz) to join plastic parts together. In the context of electric bike displays, the technology converts electrical energy into mechanical vibrations, which create friction and heat at the contact points of plastic parts. This causes them to melt and fuse quickly and cleanly, creating a strong bond without the need for glue or screws.
How Ultrasonic Welding Works
The ultrasonic welding system consists of several key components:
-
Ultrasonic Generator: Converts 50/60Hz electrical current into high-frequency electrical energy (usually 20kHz or 40kHz).
-
Transducer/Booster: Converts electrical energy into mechanical vibrations.
-
Welding Horn: Transmits vibrations to the workpiece.
-
Fixture: Holds the parts to be welded in place and applies pressure.
When the system is activated, high-frequency vibrations are transmitted through the welding horn to the upper workpiece. The friction between the contact surfaces of the upper and lower parts generates heat, causing the plastic to melt quickly. Under pressure, the melted plastic fuses, and after cooling, a strong welded joint is formed.
Advantages of Ultrasonic Welding in Electric Bike Display Applications
Comparison with Traditional Methods
When compared to traditional assembly methods for displays, ultrasonic welding offers significant advantages:
Process Parameter | Ultrasonic Welding | Screw Fixing | Adhesive Bonding |
Connection Time | 0.1-1 seconds | 30-60 seconds | 60-180 seconds |
Curing/Setting Time | Instant | Instant | Several hours |
Material Compatibility | Thermoplastic Plastics | All Materials | Most Materials |
Connection Strength | High | Medium | Medium to High |
Process Cleanliness | High | Medium | Low |
Automation Potential | High | Medium | Low |
Industry-Specific Advantages
Ultrasonic welding provides unique value for fast e bikes display manufacturing, meeting the specific needs of the industry:
-
Waterproof Performance: Creates a seamless seal that meets IP67 or even higher protection standards.
-
Vibration Resistance: The molecular-level fusion offers better resistance to long-term vibrations compared to mechanical fastening.
-
Aesthetic Appeal: No visible fasteners, keeping the display surface neat and attractive.
-
Material Savings: Eliminates the need for additional fasteners or adhesives.
-
Process Consistency: Digital control ensures uniform quality at every welding point.
Key Process Parameters for Ultrasonic Welding in Electric Bike Displays
Material Selection and Compatibility
When selecting materials for electric bike displays, it’s important to consider their suitability for ultrasonic welding. Here are some common plastics used in display manufacturing:
-
ABS: Easy to weld and commonly used for display housings.
-
PC (Polycarbonate): High strength and transparency, ideal for display windows.
-
PC/ABS Alloy: Balanced performance and good weldability.
-
PMMA (Acrylic): Used for highly transparent parts but requires special process parameters.
-
Nylon: Moisture-sensitive and requires pre-treatment.
Material Matching Principle: Materials with similar melting points weld better together. For example, an ABS-ABS combination typically results in higher-quality welds compared to an ABS-PC combination.
Process Parameter Optimization
To achieve successful ultrasonic welding, precise control of the following parameters is essential:
-
Frequency: 20kHz
-
Amplitude: 35μm
-
Welding Time: 0.3 seconds
-
Hold Time: 0.5 seconds
-
Welding Pressure: 0.4MPa
-
Hold Pressure: 0.3MPa
Joint Design
Proper joint design is crucial for ensuring welding quality:
-
Energy Director Design: Triangle-shaped protrusions (0.3-0.5mm high) at the weld surface concentrate friction heat.
-
Shear Joint: Suitable for crystalline plastics like nylon, using a stepped joint design.
-
Snap-fit Design: Provides alignment and positioning functions.
-
Near-field vs. Far-field Welding: Near-field refers to a distance of less than 6mm between the welding horn and the workpiece; beyond that is considered far-field.
Design Guidelines:
Consider mold release angles (usually 1-2°).
Quality Control in Ultrasonic Welding for Electric Bike Displays
Process Monitoring Technology
Modern ultrasonic welding equipment is typically equipped with various monitoring methods:
-
Energy Mode: Controls the total input energy (J).
-
Distance Mode: Controls the welding horn’s downward distance (mm).
-
Time Mode: Fixed welding time (s).
-
Peak Power Monitoring: Detects abnormal welding conditions.
-
Collapse Distance Monitoring: Assesses the degree of material melting.
Common Defects and Solutions
Defect Type | Cause | Solution |
Insufficient Welding | Low energy, pressure | Increase amplitude/time, pressure |
Over-welding | Excessive energy, time | Reduce parameters, check fixture |
Surface Damage | High amplitude, bad horn design | Adjust horn shape, reduce amplitude |
Misalignment | Poor part tolerance, fixture | Improve part design, better alignment |
Weak Weld Strength | Material mismatch, poor design | Choose better materials, optimize design |
Testing and Verification Methods
The quality assessment of custom ebike display welding typically includes:
-
Tensile Test: Evaluates welding strength.
-
Peel Test: Assesses interface bonding strength.
-
Cross-Section Analysis: Examines fusion quality.
-
Leak Testing (Pressure decay method): Assesses the seal integrity.
-
Visual Inspection: Checks surface quality.
- Ultrasonic Scanning: Detects internal defects.
-
Temperature Cycling (-20°C to 60°C, 50 cycles).
-
Vibration Testing: Simulates road conditions.
-
Humidity Testing (85% RH, 96 hours).
Industry Application Cases and Trends
Successful Application Cases
-
Challenge: A 7-inch touchscreen requires IP67 protection while maintaining a clean appearance.
-
Solution: A two-step ultrasonic welding process was used:
-
Welding the internal frame to the middle shell (PC material with energy director design).
-
Welding the outer screen to the middle shell (PMMA-specific welding horn with low amplitude, long process).
-
-
Results: Welding time reduced from 3 minutes with traditional adhesive to 12 seconds, with yield increasing from 92% to 99.5%.
-
Challenge: A daily production demand of 5,000 units, with cost sensitivity.
-
Solution:
-
Standardized welding parameters (single material ABS).
-
Integration of automated loading and unloading systems.
-
Quality monitoring based on Statistical Process Control (SPC).
-
-
Results: Welding cost per unit reduced by 60%, with equipment utilization reaching 85%.
Future Development Trends
-
Multi-material Welding Technology: Developing processes capable of welding different plastics and even plastic-metal composite materials.
-
Intelligent Process Monitoring: Using AI to analyze welding parameters in real-time, predict quality, and automatically adjust settings.
-
Sustainability: Solvent-free processes supporting green manufacturing and material recycling.
-
Miniaturization: Suitable for smaller wearable electric bike smart devices.
-
Hybrid Welding Technology: Combining the advantages of laser and ultrasonic welding for special material combinations.
Implementation Recommendations
For eBike manufacturers planning to adopt ultrasonic welding, the following steps are recommended:
-
Start with Small-Scale Trials: Begin by selecting non-critical components for process validation to test and refine the welding technique.
-
Cross-Department Collaboration: Involve design, materials, and process engineers early in the process to ensure smooth integration.
-
Supplier Partnerships: Work with equipment suppliers who have experience in the eBike industry to ensure the right technology and support.
-
Staff Training: Provide specialized training for operators and maintenance personnel to ensure proper handling and troubleshooting of ultrasonic welding equipment.
-
Gradual Integration: Start with simpler components and progressively transition to more complex parts as the process is optimized.
Leave a comment