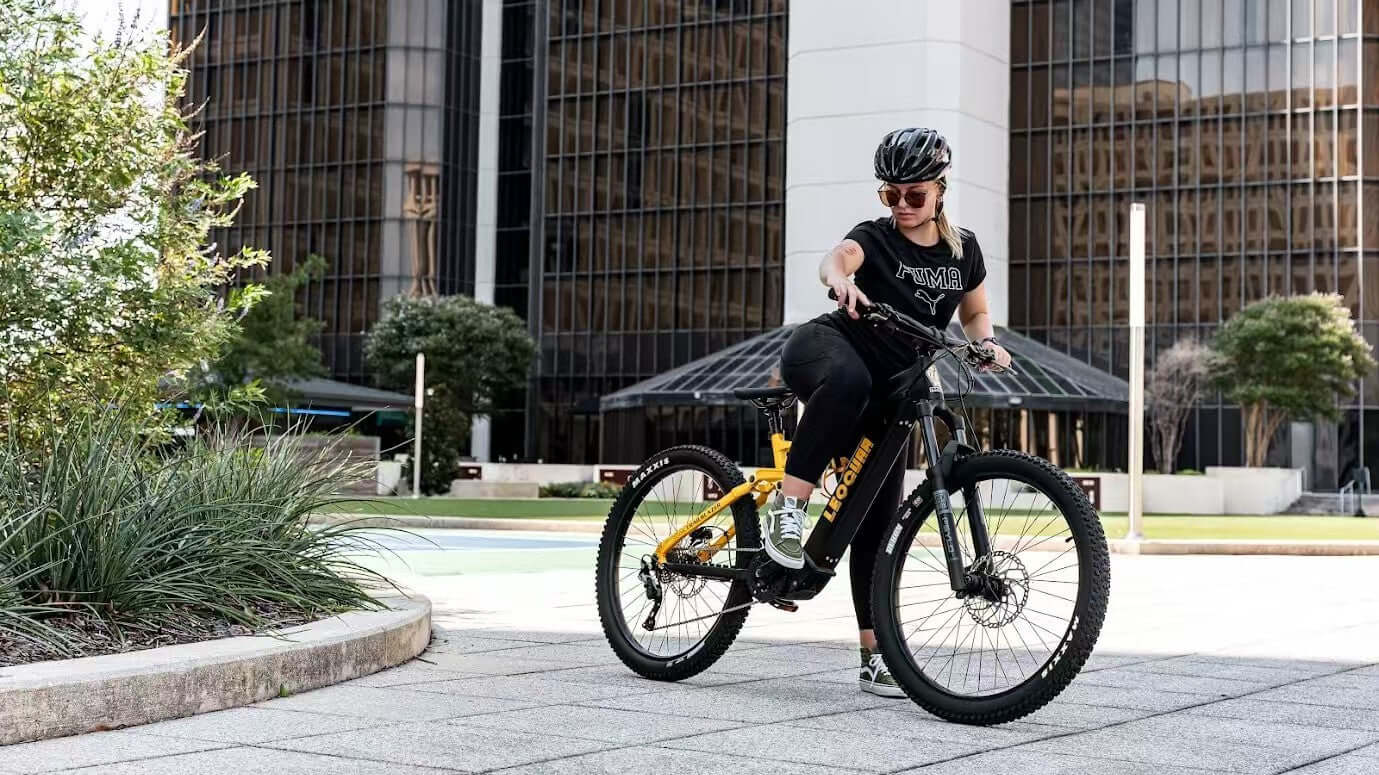
The Power Core of Electric Bikes: In-Depth Comparison of Direct Drive Motors and Geared Motors
Introduction: Why Choosing the Right Electric Bike Motor Matters
In today’s urban transportation, electric bikes (eBikes) have become a popular choice for many commuters. As the "heart" of an eBike, the motor system directly affects the bike’s performance, riding experience, and overall durability.
Currently, the electric bike market mainly offers two types of motors: direct drive motors and geared motors. Each technology has its unique strengths and is suited to different riding conditions and user preferences.
This article provides a detailed breakdown of their working principles, structural differences, performance features, and ideal applications, helping you make a smarter choice when buying an electric bike.
How a Direct Drive Motor Works
A direct drive motor connects the rotor directly to the wheel hub, eliminating the need for a gear reduction system. It typically uses an outer rotor design, where the stator is fixed to the axle and the outer rotor, attached to the rim, rotates around it.
When electric current passes through the stator windings, it generates a magnetic field that directly drives the rotor, turning the wheel. Because the motor’s rotation speed matches that of the wheel—typically between 200 and 500 RPM—direct drive motors are classified as low-speed, high-torque systems.
The structure is simple, made up of the stator, rotor, bearings, and housing. While this simplicity results in several key advantages, it also introduces some limitations.
Advantages of Direct Drive Motors in Electric Bikes
High Reliability and Long Service Life
One of the biggest advantages of a direct drive motor is its outstanding durability. With no gears or complex moving parts inside, mechanical wear is minimal. High-quality direct drive motors can easily achieve over 50,000 hours of operation under normal riding conditions. This exceptional longevity makes them an ideal choice for riders who frequently travel long distances or use their bikes for daily commuting.
Strong Efficiency at High Speeds
Direct drive motors maintain high efficiency even when the bike exceeds 25 km/h, which is the typical speed limit for eBikes in many countries. This makes them especially suitable for open-road riding where sustained higher speeds are required. Riders who prioritize speed and performance over technical climbing will benefit greatly from the consistent output of a direct drive motor.
Greater Power Capacity
Compared to geared motors, direct drive motors typically have a much higher potential for power output. Many high-performance models easily deliver 1000W or more. This allows riders to tackle demanding conditions, such as long-distance cruising or carrying heavier loads, without significantly sacrificing motor stability or reliability.
Effective Regenerative Braking
An often overlooked benefit of direct drive motors is their ability to support regenerative braking. Because the motor operates like a large generator, it can efficiently convert braking energy back into electricity and recharge the battery during long descents. This feature helps extend the overall battery range and enhances energy recovery, making the eBike more efficient over time.
Limitations of Direct Drive Motors in Electric Bikes
Weaker Low-Speed Torque
One significant limitation of direct drive motors is their relatively weak performance at low speeds. Without the benefit of gear reduction to amplify torque, these motors can struggle during starts or on steep inclines. Although applying more current can help improve torque, it often results in higher energy consumption and increased heat generation, which can impact overall motor efficiency.
Increased Motor Weight
Direct drive motors are generally heavier than geared motors of similar power levels—typically 30% to 50% more. A standard 500W direct drive motor usually weighs between 6 and 8 kilograms. This added weight affects the bike’s overall handling, makes it more difficult to carry, and can be a challenge when pedaling without motor assistance.
Magnetic Drag During Unpowered Riding
Another drawback is magnetic drag, also known as cogging resistance. Even when the motor is switched off, the permanent magnets inside create slight resistance against wheel rotation. Although modern designs can reduce this effect, it is difficult to eliminate entirely, making riding without motor assist feel noticeably heavier compared to geared motor setups.
Geared Motors in Electric Bikes: A High-Efficiency and Flexible Power Solution
Basic Structure and Working Principle
Geared motors in electric bikes typically use either an inner rotor or an outer rotor design. Through a planetary gear system or a multi-stage gear reduction setup, the motor’s high-speed rotation—usually between 2,000 and 4,000 RPM—is reduced to a wheel-friendly speed of around 200 to 300 RPM, while torque is proportionally increased.
This setup allows the motor to operate within its optimal efficiency range and adapts the output to meet the needs of the bike through mechanical transmission, ensuring strong performance at practical riding speeds.
A typical geared motor consists of a high-speed rotor, a gear reduction unit, a clutch mechanism, and a protective housing. The clutch—usually a ratchet or a one-way bearing—allows the wheel to spin freely when the motor is not engaged, effectively eliminating the magnetic drag experienced in direct drive motors.
This modular design not only improves efficiency but also offers unique advantages in freewheeling and everyday riding comfort.
Key Advantages of Geared Motors
High Torque for Quick Starts and Hill Climbs
This design allows geared motors to perform exceptionally well during start-up acceleration and hill climbing, making them particularly suitable for mountain ebikes and heavy-load eBikes.
Better Efficiency at Urban Speeds
When riding within the common speed range of 15 to 25 km/h, geared motors generally achieve 10% to 20% higher efficiency compared to direct drive motors.
Since the motor works closer to its optimal efficiency point and the gear system adjusts the output speed to match the bike’s needs, less energy is wasted.
This means that, under the same battery capacity, geared motors often provide longer riding ranges, which is a major advantage for daily commuting and longer trips.
Lightweight and Easy Freewheeling
Another notable benefit of geared motors is their lighter weight. A typical 500W geared motor weighs between 3 and 5 kilograms, making it more than 30% lighter than a comparable direct drive motor.
This not only improves the overall balance and agility of the eBike but also makes riding without motor assistance much easier.
Thanks to the built-in clutch mechanism, when the motor is not engaged, it fully disconnects from the wheel, allowing the bike to freewheel smoothly and providing a pedaling experience very similar to that of a traditional bicycle.
Technical Comparison: Key Performance Metrics
Efficiency Comparison and Application Scenarios
The efficiency characteristics of geared motors and direct drive motors differ significantly. Geared motors perform best at lower speeds (10–25 km/h), achieving efficiencies between 75% and 85%, making them ideal for city commuting where frequent stops and starts are common. In contrast, direct drive motors show greater efficiency at higher speeds (25–45 km/h), making them better suited for suburban or open-road riding.
Test data shows that at a steady speed of 20 km/h, geared motor systems are about 15% more efficient than direct drive systems. However, at 35 km/h, the advantage reverses, with direct drive motors outperforming geared motors by around 10%. This difference comes from the fact that direct drive systems avoid the mechanical losses associated with high-speed gear transmission.
Torque Output Characteristics
Torque curves clearly show the differences between the two motor types. Geared motors deliver 50% to 100% higher torque than direct drive motors in the low-speed range of 0–300 RPM (roughly 0–20 km/h), which explains their strong climbing abilities. However, once speeds exceed 400 RPM, geared motor torque drops off sharply, whereas direct drive motors maintain more consistent torque as speed increases.
For example, a typical 500W geared motor can provide 80–100 Nm of wheel torque during startup, while a direct drive motor of the same class typically delivers only 40–50 Nm. As speed climbs to around 300 RPM, the torque output of both types converges to about 25 Nm.
Noise and Vibration Performance
At low speeds, geared motors operate quietly, typically generating less than 55 decibels of noise. However, as speed increases, gear engagement noise becomes more noticeable, often exceeding 65 decibels.
Direct drive motors, on the other hand, maintain a relatively constant noise level around 60 decibels across all speeds. Most of the noise comes from wind resistance and electromagnetic operation, offering a smoother and more consistent sound profile.
In terms of vibration, direct drive motors have a clear advantage. With no mechanical transmission components, they produce minimal vibration. Geared motors may experience gear resonance at specific speeds, causing slight vibrations throughout the electric bike frame, although high-quality designs significantly reduce this issue.
Application Guide: Choosing the Right Motor for Your Needs
Ideal Applications for Direct Drive Motors
Direct drive motors are best suited for long-distance road cycling. Their high-speed cruising efficiency, low maintenance requirements, and regenerative braking capabilities make them ideal for touring and long-range commuting. Brands like RadRover commonly use direct drive motors for long-distance eBikes.
Cargo transport is another strong use case. Thanks to their high continuous power capacity and excellent reliability, direct drive motors are widely used in cargo electric bikes and delivery tricycles, especially in demanding commercial environments.
Additionally, in wet or rainy climates, direct drive motors are often more reliable. Without a gearbox, there are fewer components vulnerable to water intrusion, making direct drive systems a better choice for coastal or high-rainfall areas.
Ideal Applications for Geared Motors
City commuting is where geared motors excel. Their superior low-speed efficiency and strong torque for frequent starts and stops make them the dominant choice for urban eBikes. Leading brands like Bosch and Shimano use geared motors extensively in their commuter bike systems.
Mountain biking relies heavily on geared motors. The high torque output needed for steep climbs and technical terrain makes geared motors the standard for electric mountain bikes (eMTBs). Top brands like Specialized and Trek equip their eMTBs exclusively with geared drive systems.
Lightweight applications also favor geared motors. Folding electric bikes, city bikes for women, and any use case where lower weight is important benefit from the lighter design of geared systems. For example, the Brompton Electric folding bike uses a specially designed lightweight geared motor.
Future Trends and Innovations in Electric Bike Motors
Advancements in Direct Drive Motor Technology
Emerging winding technologies, such as fractional-slot concentrated windings, are improving torque density in direct drive motors, narrowing the performance gap at low speeds. At the same time, material innovations—like potential applications of superconducting materials—may address the long-standing issue of heavy motor weight.
Progress in smart control algorithms is also noteworthy. With optimized FOC (Field-Oriented Control) strategies, modern direct drive systems are delivering smoother torque at low speeds, improving the startup experience. Some high-end systems are even simulating "virtual gear ratios" to enhance performance across a broader speed range.
Breakthroughs in Geared Motor Technology
Gear material technology is advancing rapidly. New options like carbon fiber-reinforced composite gears and metal injection molding (MIM) gears are significantly extending gear lifespan. Experimental ceramic gears have already demonstrated service lives exceeding 50,000 kilometers.
Integrated design is another major trend. By fully integrating the motor, gearbox, and controller into a sealed unit, manufacturers are reducing overall size and boosting system reliability. For example, Yamaha’s PWseries SE system achieves full integration of motor and gearbox into a single, highly durable unit.
Exploring Hybrid Drive Systems for Electric Bikes
Some cutting-edge designs are starting to explore hybrid drive systems that combine the benefits of both geared and direct drive motors. For example, Germany’s Neodrives has introduced the Zweiseiten Motor, which uses a geared transmission at low speeds and automatically switches to direct drive at higher speeds.
Although the design is still complex and expensive, this type of system could become a direction for high-end electric bikes in the future.
Another idea being explored is multi-speed electric motors, similar to a car’s transmission. These systems use two to three different gear ratios to better match different riding conditions. Traditional drivetrain makers like Pinion and Rohloff have already developed electric-specific multi-gear systems for eBikes, showing that innovation is happening quickly.
Choosing the Right Electric Bike Motor for Your Needs
Direct drive motors and geared motors each have their own strengths, and neither is absolutely better than the other. For city commuters, geared motors are usually the smarter choice because of their lighter weight and higher efficiency at lower speeds. Long-distance riders, on the other hand, may prefer direct drive motors for their durability and stronger performance at higher cruising speeds. Mountain bikers typically rely on the powerful climbing capabilities offered by geared motors, making them the best fit for rough terrains and steep hills.
As technology continues to improve, the performance gap between direct drive and geared motors is getting smaller. When choosing an electric bike in the future, riders should pay more attention to real-world performance data rather than focusing solely on motor type. No matter which system you choose, it is the quality of the electromagnetic design, the precision of the manufacturing process, and the sophistication of the control system that will ultimately determine the riding experience.
In a world where electric bikes are becoming more popular every day, understanding these core differences can help you make smarter, more personalized choices. By selecting a motor that fits your needs, you can enjoy every ride with greater comfort, better efficiency, and more satisfaction.
Leave a comment
Please note, comments must be approved before they are published
This site is protected by hCaptcha and the hCaptcha Privacy Policy and Terms of Service apply.